2.3
Adding corrosion inhibitors to oil and gas
Among the many anti-corrosion measures, adding corrosion inhibitors is the only measure that does not need to change the
flange. The addition of corrosion inhibitor can make the conveying medium form a layer of anti-corrosion film on the inner surface of the flange and pipe wall, slow down and prevent the contact between the medium and inner wall, thereby slowing down corrosion. Corrosion inhibitors are currently divided into two categories: inorganic corrosion inhibitors and organic corrosion inhibitors. In actual use, the use environment and characteristics of the transport medium should be comprehensively considered to select the corrosion inhibitor. Adding corrosion inhibitors is relatively simple and efficient, but at the same time, the corrosion inhibitor is easy to flow with the conveying medium. Dosages, filling cycles and filling methods of corrosion inhibitors should be strictly controlled. Otherwise they will not only affect the performance of the corrosion protection function, but also affect the transmission and flow of conveying media.
2.4
Anti-corrosion treatment at the gap
At present, there are various anti-corrosion treatment technologies for flange gaps. A relatively old solution is to use stainless steel or other materials, coupled with rubber strips to protect the outer cover and fixtures to seal the gap between the flange and flange surface. However, this traditional scheme is relatively inflexible, mainly because covers and fixtures with various sizes are required to match various flanges. Another relatively commonly used and reliable solution nowadays is to use anticorrosive tapes such as petrolatum tape, wax paper and elastic polymer bandages. The tape can be wound on outer surfaces and gaps of the flange to protect the flange. Because the anti-corrosion tape has relative good airtightness and waterproofness, they can provide relatively reliable anti-corrosion protection for flanges. In addition, there are viscoelastic materials 7, hot melt plastics and other materials which can also play a good anti-corrosion effect on surfaces and gaps of flanges by filling flange gaps and surfaces.
2.5
Anti-corrosion measures for dissimilar metal flanges
There is often a metal connection at the flange part, and there is a risk of galvanic corrosion. In view of this, the installation of insulating gaskets and the surfacing treatment of low-potential metal flanges are two effective measures to prevent galvanic corrosion. They are also relatively two measures which are feasible and convenient for construction in the ISO 21457 Standard section 8.7 related to galvanic corrosion.
2.5.1
Installing insulating gasket assembly
The components of the insulating gasket assembly are shown in Figure 1. Installing insulating gaskets on the flange contact surface and contact surfaces between the bolt and flange can effectively control the galvanic corrosion of the flange caused by dissimilar metals. The direct contact of dissimilar metals is isolated, so that galvanic corrosion minimizes for the entire flange assembly. It is inevitable. There are still dissimilar metal connections in the grounding wire and other locations. However, the galvanic corrosion caused by them is very little, which is an effective measure to control the galvanic corrosion of the flange surface.
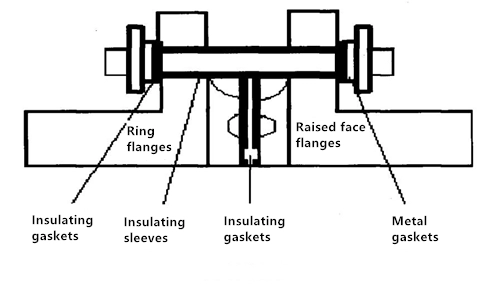
Figure 1 Insulating gasket assembly
2.5.2
Surfacing of corrosion resistant alloys on the flange sealing surface
Overlay welding of corrosion resistant alloys on the flange sealing surface is an anti-corrosion technology that uses welding methods like electrode arc welding to overlay the corrosion-resistant alloys materials on the flange sealing surface. This measure can transfer the galvanic corrosion to insides of the entire pipeline. Combined with the injection of corrosion inhibitors, galvanic corrosion can be effectively controlled and the flange sealing surface can be effectively protected; galvanic corrosion caused by dissimilar metals can be avoided to a large extent.
2.6
Human factors
Among the many corrosion factors for
flanges, the human factor is the most controllable factor. By strengthening internal management, improving the quality of personnel, frequency of equipment inspections and quality of inspection and maintenance, etc., flange corrosion conditions can be discovered in time, and timely dealing with the problem and good maintenance can be obtained. For example, in view of flange corrosion caused by oil water separation in oil and gas pipelines, measures such as intermittent great flow transportation, optimizing frequency of pigging operations, etc., can be used to improve quality of the transported medium, and human measures like increasing frequency of removing the water trapped in the flange gaps to prevent and slow down flange corrosion.
3. Conclusion
Among the many factors affecting flange corrosion, internal corrosion is the main reason for flange leakages. Because internal corrosion is related to and affected by flange surface roughness, flange materials, conveying media and various chemical parameters, understanding of the exact mechanism and specific problems of its corrosion and development of future anti-corrosion technologies are still very challenging subjects. Practice has proved that regular maintenance of pipelines and valves and strengthening of pipeline daily management are simple and efficient measures which can greatly improve corrosion resistance of oil and gas storage and transportation pipelines. The reliability and stability of flanges in long-distance oil and gas pipelines have been issues that we have to pay attention to for a long time. Research institutions and enterprises must develop and introduce more effective anti-corrosion protection systems. Only through continuous innovation and development can the safe operation of long-distance oil and gas pipelines be ensured.